The safety and reliability of medical device packaging is important. For that reason, packaging designs must meet strict requirements and undergo comprehensive validation before they obtain approval for the market. Ensuring your packaging system follows industry standards is the key to developing solutions that protect devices and maintain sterility throughout the supply chain.
There are several guidelines to follow when designing and testing medical device packaging used to enclose the reusable devices found in our healthcare system. Let’s take a look at different medical device packaging standards, and explore the role they play in developing packaging solutions.
ISO 11607
The International Standards Organization (ISO) offers a multitude of guidelines for products and workflows across various industries, including health care. This includes a set of guidelines for packaging validation. ISO 11607 is a standard that outlines requirements for packaging materials and designs. Following these instructions assists in the proper design and validation of sterile packaging systems.
ISO 11607-1
The ISO 11607 standard is split into two main parts. Part One revolves around a packaging system’s sterile barrier system. It outlines requirements for establishing the sterile barrier, including material requirements. It also discusses proper material selection, stating that materials must be nontoxic and free of defects. They must also consist of traceable components and should be intended specifically for use in and around medical devices.
ISO 11607-1 also discusses overall packaging design and validation. This includes testing methods to discover defects and ensure an effective sterile barrier and strong seal for the packaging. The standard covers testing methods, including visual inspection, bubble leak tests, and microbial challenge tests, to ensure the quality of device packaging materials and designs.
ISO 11607-2
Part Two of the ISO 11607 standard covers requirements for the overall packaging process. The guidelines in ISO 11607-2 help with the design and validation of processes such as forming, sealing, and assembling sterile packaging systems typically seen when manufacturing single use medical devices. Following this standard ensures that a packaging system’s sterility barrier is the result of high-quality manufacturing and assembly.
Both parts of ISO 11607 work together to guide the responsible design of medical device packaging. This allows for successful production and ensures both the packaging and the device remain sterile during shipping, handling, and storage.
International Safe Transit Association (ISTA)
The Food and Drug Administration (FDA) also recognizes standards from the International Safe Transit Association (ISTA) regarding the safety and sterility of medical device packages while in transit. All packaging must maintain its sterility barrier until it is ready for use. This means the packaging must have the integrity to stand up to movement and environmental factors during shipping.
ISTA standards offer guidance for testing procedures to ensure device packaging can withstand factors such as:
- vibration
- shock
- extreme temperature fluctuations
- pressure fluctuations, and
- extreme humidity levels.
These standards help manufacturers develop medical device packaging that will remain sterile and safe for use after transit.
AAMI ST-77
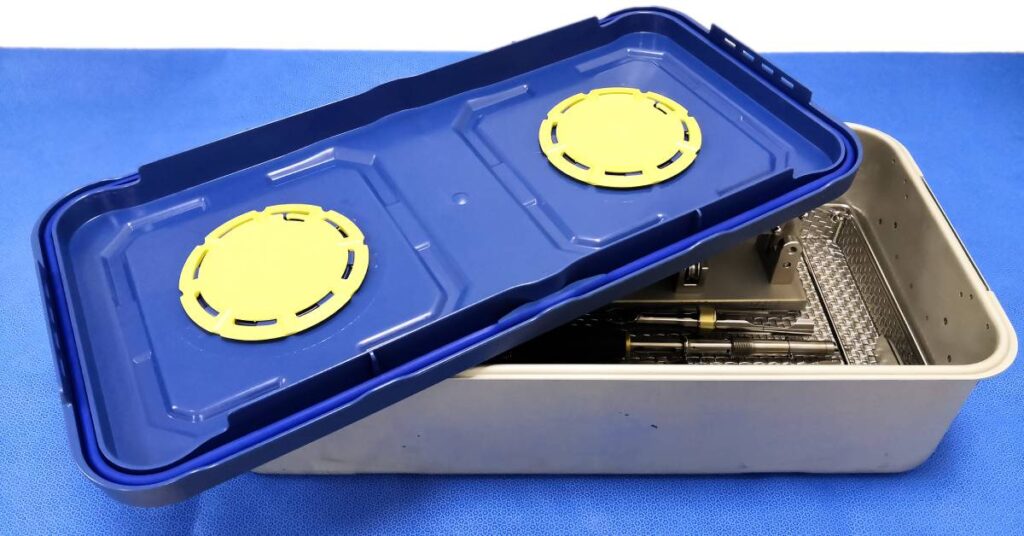
Another important medical device packaging standard to look at is the Association for the Advancement of Medical Instrumentation’s AAMI ST-77. This discusses the necessary requirements for rigid sterilization containers and other containment devices to offer adequate sterilization and sterility maintenance for the instruments they contain.
This standard addresses material durability to prevent cracking, flaking, peeling, corrosion, and other forms of deformation. It also covers packaging compatibility with the sterilization process by stating that the materials making up the containment device must suit its sterilization and drying processes. Finally, ST-77 addresses biocompatibility so selected materials do not affect the safety and performance of the packaging system or the reusable medical device it contains.
AAMI ST-77 also offers a performance standard for reusable medical device packaging systems. This includes setting a weight limit on containment devices to address safe use, sterilization capabilities, and healthy ergonomics for end users.
FDA General Labeling Requirements
The FDA also maintains general labeling requirements for all medical devices. Printed wrappers, tags, pamphlets, and other messaging or marketing materials must comply with FDA regulations.
One requirement is that the label must include the name and location of the medical device’s packer or distributor and the original manufacturer. This includes their street address, city, state, and zip code. The label must also include information about the intended use of the medical device. Finally, the labeling needs clear, straightforward directions for use that the average person can safely follow.
FDA labeling requirements also outline mislabeling practices to avoid, including the following:
- printing misleading statements on the label
- failing to display information on parts of the packaging that are customarily displayed during purchase and use
- taking up too much space with non-labeling information and being unable to fit labeling information on the package
- printing illegible labeling information due to printing mistakes or design inefficiencies
Avoiding these mislabeling practices helps create clear, coherent labels on medical device packaging and medical device packaging systems. This makes it easier to obtain market approval and deliver safe, usable packaging and products to end users.
Other Factors To Consider
Though these standards are important, they don’t cover every consideration manufacturers need to make for their medical device packaging systems. There are other factors to address when developing packaging designs for market approval, including shelf life, storage conditions, and ease of use.
Shelf Life
Defining the shelf life of a reusable medical device and its packaging system is crucial to guaranteeing its efficacy and safety. If the packaging system cannot maintain integrity for the entire duration of the device’s shelf life, it does not offer reliable sterility and is therefore invalid for use.
Storage Conditions
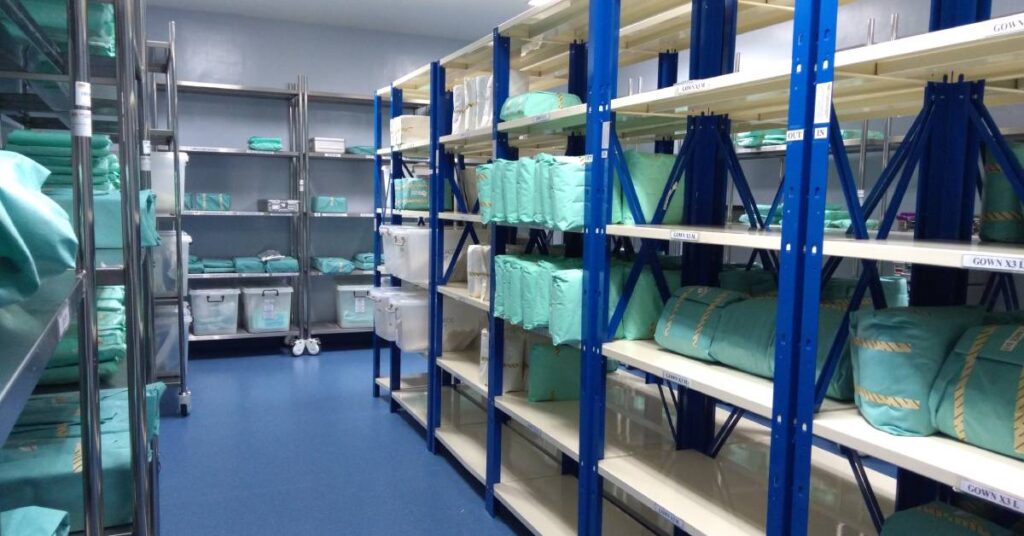
Manufacturers must also take the intended storage conditions of a reusable medical device into consideration when designing packaging systems. If the device has specific storage requirements, such as ultra-low temperatures or extremely dry conditions, the packaging must also be able to withstand those temperatures. Careful consideration and testing are necessary to select materials and designs that do not crack, shrink, or otherwise lose their sterility in these conditions.
Ease of Use
Medical device packaging must also be easy to use. This means it should be easy to open without damaging the device or risking contamination. Designing packaging that is simultaneously robust enough to withstand shipping and intuitive enough for easy use is the key to delivering effective and worthwhile medical device solutions to end users. To achieve this, packaging validation testing must include opening the device under sterile conditions to ensure end users can open the package and remove the device without contaminating it.
Highpower Labs Offers Medical Device Packaging Validation
Packaging design validation is a key part of developing safe and effective medical products. Highpower provides medical device package testing to determine whether a packaging system follows industry standards and meets the needs of real-world health-care settings. Learn more about our packaging validation services today, and let Highpower help you on your way to standard approval.